April 2008 Edition
larger margin
Dennis G. Seeds
Editor-in-Chief
Team execution . . .
. . . vs. revolutionary strategy
If you look deep enough into the recent speech General Motors
President and COO Fritz Henderson gave to the Automotive Press Association, you
will find some encouraging words.
The company, if you haven’t heard, has racked up North
America losses for nearly two years in a row — losing $38.7 billion last year.
But since cutting down on operating costs and boosting sales overseas (59
percent of 2007 sales were in countries other than the United States), GM has
made progress with this strategy.
"This is not a business known for revolutionary strategy —
it’s about who executes best," Henderson said.
Few of us in today’s automobile world were around to
remember, but I would say the last revolutionary strategy put into practice in
the auto industry was the assembly line in 1908. One hundred years ago, a couple
of Ford Motor Co. employees put a Model T frame on skids, hitched a towrope to
the front end and pulled the frame along until axles and wheels were put on.
Then they rolled the chassis along the primitive assembly line in segments while
parts were added. Some pieces, such as a radiator with its hoses, were assembled
in the background and then installed at the appropriate time.
It all made sense, and over the next five years was
perfected. The $825 Model T dropped to $575 by 1914. To put that in perspective,
the purchasing power of $575 in 1914 is comparable to $12,303 today. That’s
still a sizeable slice of a consumer’s income today, but in time, even that $575
price dropped.
When one starts to analyze this revolutionary strategy, it’s
obvious that it took time to properly execute the process. The engineers
observed that complex parts needed longer time to be installed. Yet, the line
had to keep in motion. Intervals were established to take this into account.
This took considerable trial and error. There were no computers to design a
virtual assembly line. Eventually, the supply of parts and the start-and-stop
intervals along the line meshed into a synchronized operation.
It’s amazing to think that 100 years later, automobiles are
still manufactured the same way. Robotic machines are replacing manual labor,
but the assembly process is still the same. Automation has been a method to make
the assembly line more efficient, and can’t really be considered a revolutionary
strategy. Automation is, in effect, part of what accomplishes the best
execution.
America is the world’s largest and most profitable automobile
market. It didn’t get that way by accident — it was a combination of many
factors. In simplest terms, it was because automakers executed their operations
successfully, perhaps excepting the recent struggles. In the early years, autos
were practical and basic. Soon, demand increased for bigger and better vehicles.
Automakers responded. After World War II, automobile style and design went
dramatic — remember the fins on the 1959 Cadillac? Automakers responded to the
demand for near-outlandish styles. Then there was the Edsel, and that design —
as well as the car — was a flop. The horse-collar grille was obviously not a
good idea on this modern horseless carriage.
For many years, the United States had a corner on
the market of manufacturing execution. No other country could
manufacture as many products so well as America could. Foreign
competition arrived on the scene and put a dent in sales by U.S.
automakers. Soon, cooperative ventures arose, and now critics are
sizing up the percentage of parts both foreign and domestic in a
vehicle.
That all makes good fuel for some debates, but it’s hard to
avoid the realization that fuel efficiency in the future will take center stage
more than ever.
Having driven a hybrid vehicle recently for a weekend, I was
impressed with all aspects of the auto. And it felt good getting 50 miles to the
gallon — that I was doing something for the future.
In addition, I was impressed that the automaker had designed
such an outstanding vehicle; it was an example of executing an idea the best way
possible.
Fritz Henderson is right. Revolutionary strategies aren’t going to take the
auto industry down the road to domination — it all comes down to who executes
best, who takes an idea and builds the team to make the dream happen.
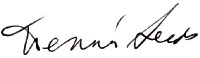
What do you think?
Will the information in this article increase efficiency or
save time, money, or effort? Let us know by e-mail from our
website at
www.ToolingandProduction.com or e-mail the editor at
dseeds@nelsonpub.com.