February 2008 Edition
IMTS readers' choice
Cutting-tool innovations
Tooling & Production has invited IMTS 2008 exhibitors
to share their latest innovations with readers before the
doors of Chicago's McCormick Place open in September. This
month, T&P focuses on cutting-tool products.
In the coming months, T&P will feature inspection
products, software, laser and waterjet marvels, abrasive
machining products, and the best in turning and machining.
CoroMill 490
In anticipation of IMTS 2008, Sandvik Coromant will
release the CoroMill 490 in March. The first in a new family
of versatile shoulder milling tools, the CoroMill 490 will
cut the cost of face and shoulder milling operations in
small to medium batch sizes.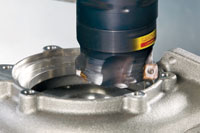
The CoroMill 490 offers lower tool costs, reduced tool
inventories, greater flexibility, higher precision, and
better tolerances. The CoroMill 490 features four-edge
inserts with outstanding geometry design and new grades. The
state of the art CoroMill 490 insert design produces less
cutting force on the component, providing better operational
stability while requiring less horsepower. This results in a
smoother profile and reduces the amount of machining time
spent on finishing.
To minimize tooling inventories and operational expenses,
the CoroMill 490 was designed to excel in a wide variety of
milling operations. The tool can be used for contouring and
edging, semi-finish and finish boring with cylindrical or
helical interpolation, and slot milling. By providing high
performance across a spectrum of milling applications, the
CoroMill 490 can replace expensive stocks of specialized
tools and simplifies production control.
The CoroMill 490 maximizes the potential of Sandvik
Coromant's New Insert Generation milling grades. Combined
with unique geometries, these new grades machine high
quality component in a productive, dependable and
predictable way, while holding tight tolerances. The new
edge geometry provides better surface finishes and tighter
tolerances on milled components, and good chip evacuation.
For more information on
Sandvik Coromant
SUMO TEC
Iscar Metals Inc. is introducing a revolutionary new
metalworking concept for increased productivity called 3P
SUMO line. This concept presents Premium Productivity
Products (3P) "for better productivity, better
profitability, and better performance."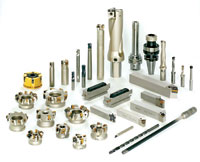
The highlight of the 3P product introduction is SUMO TEC,
which features a new series of premium tungsten carbide
grades to meet the contemporary machining challenges of the
metal cutting industry.
The new series of carbide grades will excel metal cutting
performances to new achievements in drilling, milling,
turning, and grooving applications. Complementing SUMO TEC,
Iscar has developed a new series of tools and inserts
branded SUMO lines.
The new exclusive grades significantly extend insert tool
life as a result of a unique innovative substrate
scientifically engineered by ISCAR. In addition, the SUMO
TEC grades feature the most advanced coating technology
using the CVD and PVD processes. Behind the PVD process is
Iscar's AL-TEC coating technology. The CVD coating is based
on Iscar's ALPHA-TEC technology, which has proved to be
superiorly resistant to wear. This unique process provides
improved tool life, low insert surface stresses, and an
evenly coated top surface. The even surface contributes to
smooth uninterrupted chip flow, less generated heat and less
friction. The new process improves toughness and chipping
resistance, thus reducing friction and built-up edge, which
in turn prolongs tool life at increased machining conditions
for all types of workpiece material.
For more information on
Iscar Metals Inc.
Milling cutter
Walter
recently updated the F2330 milling cutter with Trigon-cutting
inserts. The F2330 used previously in standard milling
operations has been improved to work with difficult
machining operations such as circular interpolation,
plunging, and pocketing. Mechanical engineering companies,
mold designers and specialists in the processing of turbine
blades will benefit. These inserts have three cutting edges
and a positive basic shape guaranteeing a soft,
low-vibration cut. For fine-tuning the application, three
cutting geometries are available: universal, stable and
easy-cutting. The tool bodies, available in diameters from
0.750" to 4.000", utilize wide flutes in order to avoid chip
packing.
Similar to the Tiger-tec cutting materials, WKP25 and
WKP35, Walter is currently delivering cutting inserts for
the F2330 from the new PVD Tiger-tec types WSP45 and WSM35.
These cutting materials have been specifically developed for
the manufacturing of stainless steel or low machinability
alloys such as titanium. These new developments provide an
expanded range of application for high-performance tools,
increased cutting speeds and longer service life in
difficult to machine applications.
For more information on
Walter AG.
4E geometry debuts
ATI Stellram specifically designed the 4E Turning
Geometry to meet the demands of machining aerospace-type
components, manufactured from high nickel, high cobalt and
titanium-based alloys.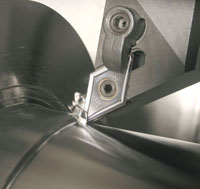
Available in new grade SP0819, 4E inserts utilize an
approved aerospace substrate, and are enhanced with a Nano
TiAIN layer PVD coating for unmatched performance.
ATI Stellram's new 4E Aerospace Turning Geometry provides
- Longer tool life. The 4E's combination of a new
super-hard coating with micro-grain carbide substrate
significantly improves heat and wear resistance in high
temperature alloy machining, enabling longer tool life
and higher productivity.
- Improved component quality. The 4E's new precise
reinforced chipbreaker profile with positive cutting
action dramatically reduces built-up edge, leaving a
smooth surface finish and greater component dimension
integrity.
- Application versatility. The 4E is designed to
machine a wide variety of materials including stainless
steels, high nickel, high cobalt and titanium-based
alloys, helping to reduce inventory, operator error, and
cost.
For more information on
ATI Stellram
Custom tools
Advent
Tool & Manufacturing announces the creation of a new
company, TMFM LLC, an Advent Tool affiliate formed to
specialize in spline, form and custom milling tools. Because
of recent progress with new and innovative designs,
including their recently patented spline form milling tools,
TMFM LLC is pursuing the further development and refining of
specialized milling tools in these new and developing
fields.
Advent Tool & Manufacturing, Lake Bluff, IL, has been
manufacturing solid carbide, carbide-tipped, and indexable
carbide thread for milling tools since 1974.
For more information on
Advent Tool & Manufacturing
Tool analysis
Scientific
Forming Technologies Corp. announces the release of
DEFORM-3D, version 6.1. DEFORM is used by cutting-tool
manufacturers and other major manufacturers to analyze the
influence of tool design and cutting parameters on machining
performance.
DEFORM is a finite element-based system that can predict
chip form, cutting forces, temperatures, tool wear, and
other parameters based on cutting tool geometry, feed,
speed, depth of cut, and coolant.
The DEFORM material library contains more than 50
materials, including common grades of steel, titanium,
aluminum, and superalloys. Release 6.1 includes several new
materials. On the numerical side, the system features a new
mesh generator for improved run times, increased robustness,
and accuracy.
For more information on
Scientific Forming Technologies Corp.,
Parallel drill programs
Toolmaker
Mikron Tool SA Agno now offers the customer two parallel
drill programs with the ideal cost-performance ratio for
every application.
The CrazyDrill, a highly successful market introduction,
which proved itself in tests and actual production millions
of times, is the small drill for the most demanding
requirements. It is used where large series, multiple
drillings per workpiece and difficult conditions are the
norm. Depending on design, these high-performance drills are
available from stock in diameters ranging from 0.4mm to 6mm
(in 0.5mm-increments) and lengths of 2 x d to 15 x d.
The MiquDrill line is an entirely new range of products
offered by Mikron Tool. Three types of drills are available:
center drills in various diameters from 0.5mm to 6mm that
center for the smallest drilling diameters starting at 0.1mm
while simultaneously performing a 90° or 120° chamfer. The
short drill MiquDrill 200, drills holes of approximately. 2
– 3 x d. As a pilot drill, it guarantees the precise
execution with the MiquDrill 210, for example, and achieves
the precision needed in deeper hole drillings. Both drills
were especially designed for micromachining and are
available uncoated in diameters down to 0.1mm, coated from
0.3mm.
For more information on
Mikron Tool SA Agno,
Disc-milling products
Seco Tools Inc. announces the new SNHQ and LNK-05 insert
additions to its family of disc-milling products, which
consists of a wide range of carbide grades and geometries
for a variety of slotting, facing, circular interpolation,
and circlip grooving applications in any material. Both the
SNHQ and LNK-05 offer up to four cutting edges per insert
and offer wiper flats for applications requiring a
high-quality surface finish. Coupled with its extensive
lineup of cutter bodies, Seco's disc-mill families are among
the most complete in the industry.
The
SNHQ line is made up of robust inserts that are free cutting
and are less prone to tool chatter. Like the 335.19 inserts
they replace, the SNHQ inserts fit Seco's 335.19 fixed
pocket cutter bodies. The new line offers corner radius
options from 0.008" - 0.236" in right- and left-handed
styles.
Like the SNHQs, the LNK-05 inserts are also offered in
both left- and right-hand cutting configurations. The LNK-05
inserts are designed to provide low-cutting forces to deal
with longer overhangs or other unstable machining
conditions. Corner radii range from 0.016" - 0.156". Tests
with the LNK inserts have produced consistent surface
finishes finer than Ra<60 µin.
New, slimmer cutter bodies have been added to accommodate
machining narrower slots with the LNK-05 inserts (0.315" -
0.394"). Like its predecessors, the new cutters are
available in both fixed and adjustable pocket
configurations.
For more information on
Seco Tools Inc.,
Air-actuated bore tooling
Valenite LLC has introduced a new MODCO Air Actuated
Cylinder Bore (AACB) tool concept to its lineup of
engineered tooling systems. The developed technology is
designed to maximize tool life, enhance part quality, and
eliminate the need for manual adjustments and the error
potential associated with operator-made compensations.
The
tool not only eliminates drag marks caused by tool
withdrawal, thus enhancing quality, but also makes true
in-process automatic tool point compensation a practical,
economical reality for high-precision applications on CNC
machines. And, because of the resulting improvements in tool
life, the system can actually help reduce the number of
dedicated machine tools required to complete semi-finish and
finish boring operations.
The AACB the system is scalable to as small as 8mm
diameter, and can be used for virtually any boring
application where precision, tight tolerances, cylindricity,
and repeatability are essential.
At the heart of the Valenite AACB tool are three insert
cartridges, set to cut the semi-finish bore, and a fourth
insert cartridge for finishing — a pivoting cartridge that
expands outward to the finish diameter size when actuated by
spindle air.
The new system has demonstrated operational performance
that results in bores with cylindricity measuring under 10
micron, repeatable on diameter to within 1µ while allowing
for precision adjustments of the tool point in 5? increments
to compensate for insert wear to help keep maintenance
requirements low, and can be designed to allow use of
internal coolant at up to 25 bar pressure. The system can
utilize CBN and PCD inserts for high-speed applications.
For more information on
Valenite LLC,
Chamfer mill
BIG Kaiser Precision Tooling Inc. introduces the C-Cutter
Mini, an ultra-high-feed chamfer mill. The C-Cutter Mini's
compact design reduces the cutting diameter to the lowest
limit, helping to achieve ultra-high spindle speeds and
feeds.
The C-Cutter Mini delivers multifunctional cutting,
including chamfering, back chamfering and face milling. Its
high-speed back chamfering capability reduces hand
de-burring, and face milling is possible with a 45 degree
chamfering type with 0.394" square insert.
The
C-Cutter Mini is available in single insert and four-insert
designs. The single insert design utilizes the world's
smallest 0.197" square insert with four cutting edges for
smaller 45-degree chamfers and a slightly larger insert for
30- and 60-degree chamfers.
The four-insert design permits 45-degree chamfering for
diameters 0.433"-1.654". Its "triple effect" design combines
four inserts for higher feed rates, a compact diameter for
increased spindle speeds, and a new wear resistant multi
layer PVD coating for increased cutting speeds. In one
example, these factors helped the four-insert C-Cutter Mini
achieve 13 times better cutting efficiency than a
competitor's three-insert cutter.
BIG Kaiser Precision Tooling is a leader in
high-precision tooling systems and solutions. With brands
including Kaiser, BIG Daishowa, Speroni, Unilock, Sphinx,
and more, BIG Kaiser's line is focused on extreme accuracy
and repeatability.
For more information on
BIG Kaiser Precision Tooling Inc.
Thread mills
Emuge Corporation's SHUR-THREAD GFI Series of solid
carbide thread mills are now available with internal coolant
supply. By precisely applying coolant where it is needed,
waste is eliminated and chips are efficiently evacuated.
SHUR-THREAD offers high confidence machining, up to 2xD
length of cut and other technologically advanced features.
Offering an exceptional balance of performance benefits and
price, the tooling line provides superb value for any size
machine operation or production volume.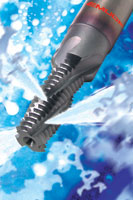
Emuge's SHUR-THREAD series combines cutting-edge design
elements with state-of-the-art grinding techniques for
enhanced performance, versatility, reliability and
ease-of-use. Featuring premium micro-grain carbide and TiCN-coated
for exceptionally longer tool life, the thread mills are
engineered with multiple spiral flutes to eliminate chatter.
Also, a large cutter diameter with high profile correction
ensures true-to-gauge threads, and an extended milling
portion allows for up to a 2xD length-of-cut. To further
enhance performance, an enlarged flute space provides
efficient chip evacuation and an end mill-type shank with
clamping flat allows for secure tool holding.
SHUR-THREAD cutters produce threads for applications 1"
and under in a wide range of soft and pre-hardened steels to
58Rc, stainless steels, aluminum, cast iron, titanium,
Inconel, and difficult to machine exotics.
The SHUR-THREAD program consists of 20 tool sizes in two
styles, type GFI and EZFI, and are available from stock.
Type EZFI is for thread sizes # 4 - # 6 - # 8, and type GFI
is for thread sizes #10 through 1.0".
For more information on
Emuge Corp.,
Aerospace tools
With orders swelling for the latest new aircraft and
promised delivery dates looming, commercial aircraft
builders have been seeking new ways to keep up with part
production schedules. Many current aircraft manufacturing
programs focus on quality, weight reduction, and cost. If
all three priorities can be addressed simultaneously in the
early stages, costs can be minimized from the start. This
was the approach taken by MAG Maintenance Technologies and
MAG Cincinnati when they partnered with a major U.S.-based
commercial aircraft manufacturer to develop equipment,
cutting tools, and processes that would significantly reduce
the cost per piece of machining titanium.
After several years of intensive development, these goals
have not only been met, but in some cases, greatly exceeded.
Productivity is up to four times the level of what had been
experienced previously. MAG Cincinnati and MAG Maintenance
Technologies are the exclusive suppliers of Technicut
tooling, and the Maintenance Technologies' Productivity
Solutions group worked with UK-based Technicut Ltd., a
brazed-carbide and solid carbide tooling application expert,
to develop the solutions.
A brazed-carbide plunger roughing tool was engineered to
deliver a unique combination of high wear resistance at the
cutting edges and toughness in the body to absorb the high
levels of vibration associated with titanium cutting. A 2"
OD cutter, for instance, with an 8" projection and a
step-over of only 0.5", is now accomplishing titanium metal
removal of over 5cu"/min. This is typically quadruple the
normal capabilities of HSS.
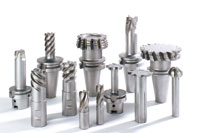
A breakthrough came with a milling cutter dubbed the
"Raptor," used for semi-finishing or finishing, as well as
roughing in some situations. The Raptor mill is achieving a
titanium removal rate of a startling 9cu"/min ... and
finishing the part in a single operation. In other aerospace
applications, the brazed-carbide Raptor has provided up to a
30X productivity bonus, with tool life doubled.
MAG Maintenance Technologies also formulated a
multi-flute brazed carbide finisher, dubbed the "Dreamcutter,"
that has proven to be successful on finish cuts on thin wall
applications of 8" deep with weight-saving wall thicknesses
of 0.060" thick. The Dreamcutter carves 8" pockets
productively with no visible steps over its entire length,
and with maximum thickness variance of 0.005".
A fourth MAG cutting tool product, the Mega-Flute, is
applied to finishing operations on many aircraft programs
using titanium and high tensile alloys, and has achieved
significant cycle-time productivity gains through the
ability to feed at over 100"/min., sustain a material
removal rate of 3cu"/min. while comfortably achieving over 1
hour of continuous cutting.
For more information on
MAG Cincinnati,
For more information on
MAG Maintenance Technologies,
FM Series
Feather
Blend is a special patented geometry that reduces the
ledging that occurs in step-down milling. This geometry is a
smooth transition from the neck diameter to the cutting
diameter of the end mill that eliminates steps and
mismatching of side walls when multiple axial depths of cut
are required. Feather Blend is helpful for insuring
structural integrity and eliminating sharp corners on
machined parts.
RobbJack's patented Mirror Edge geometry causes process
dampening of aluminum material by matching the part
frequency to the natural frequency of the tool. By doing
this, more material is removed without increasing chatter.
This geometry is also great for tools with long diameter to
length ratios because the farther a tool sticks out of the
spindle, the more inherent flexibility and, subsequently,
the more chatter. Mirror Edge can eliminate this problem. It
is also great for reducing chatter in thin wall aluminum
parts.
RobbJack FM Series is the most advanced tooling system
available to maximize high-speed machining center
investment.
For more information on
RobbJack Corp.,
Face-milling system
With a steel and aluminum body construction that offers
reduced weight, improved rigidity and vibration-dampening
characteristics, the KSCM AluMill face-milling system from
Kennametal is designed to achieve high speeds and
high-productivity results, especially for high-volume
aluminum milling operations.
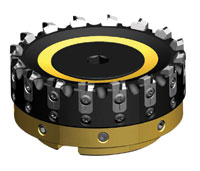
In particular, automotive applications such as engine
blocks and cylinder heads can benefit from the KSCM AluMill
system's design and performance.
KSCM AluMill cutters are available between 2.5" and 12"
(63mm and 315mm) diameters and can accommodate five
different cartridge styles for rough and finish cutting in
the same operation or for defined surface-finish
requirements. With easy cartridge insertion and adjustment,
maximum runout error is 3mm. Reduced weight and the ability
to be precision-balanced also serve to extend tool life.
For more information on
Kennametal Inc.,
What do you think?
Will the information in this article increase efficiency or
save time, money, or effort? Let us know by e-mail from our
website at
www.ToolingandProduction.com or e-mail the editor at
dseeds@nelsonpub.com.