July 2008 Edition
hot markets review: medical
Precision is the word in orthopedic implants
Device manufacturers gain solutions for accuracy, expediency
The Makino a61 is widely used in North America to make complex medical
parts.
The Japanese call it seiki. Germans call it
präzision. And to the English-speaking world, it’s precision.
Two medical device manufacturers recently found it was possible to achieve
the highest obtainable precision. One was able to bypass expensive
hand-finishing to save time, and the other saw its part cycles completed 40
percent faster.
All manufacturers strive for precision, but the word takes on new meaning for
manufactured components of implantable medical devices. Even the slightest
machining error or deviation from the design can have a severe impact. Such an
error might not become evident for years after implantation, when the
consequences are likely more serious to face.
For McMurray, PA-based FPD, a knee implant made of cobalt chromium-molybdenum
alloy required time-consuming and expensive hand finishing. The part was
especially challenging due to tight tolerances, sweeping geometries, and a fine
surface finish.
All manufacturers strive for precision, but the word
takes on new meaning for manufactured components of implantable
medical devices. Even the slightest machining error or deviation
from the design can have a severe impact.
Previous manufacturers used grinding to complete the part, but often
struggled with the complex features. FPD felt the parts had to be milled to be
consistent — again, where precision comes in.
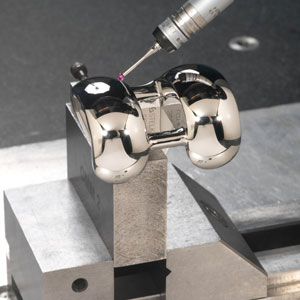
This
knee implant of cobalt chromium-molybdenum alloy is made by FPD.
After installing a Makino a61 horizontal machining center, FPD was on the
road to precision. The machine was able to take complex geometries and demands
for tight tolerances to finish the part so well that it didn’t need
hand-finishing.
In addition, FPD was able to meet high production demands from its customer
for the knee implant.
Another example is Brown Precision of Huntsville, AL. Brown was an aerospace,
five-axis part producer, but wanted to apply its skill to the medical industry.
Brown Precision knew a five-axis machine with accuracy in harder materials, such
as 316 forged stainless steel, would be needed.
Again, the call went out for a Makino a61.
Since installing the a61, parts can now be finished in single setup. For
instance, it’s a simple method to set up a forged stainless steel bone plate,
which once took several setups to complete.
With the Makino a61, Brown Precision saw a 40 percent decrease in cycle time
for the part. The company now owns several a61s, an a51, and other Makino
machines for medical device and instrument manufacturing.
Makino
What do you think?
Will the information in this article increase efficiency or
save time, money, or effort? Let us know by e-mail from our website at
www.ToolingandProduction.com or e-mail the editor at
dseeds@nelsonpub.com.
editor's blogs
Off the Toolpath
EASTEC marks 30th show with spotlight on medical devices
The recession hasn’t stopped business, if the activity at the EASTEC Advanced Productivity Exposition is to judge. The show, in its 30th year, drew 570 exhibitors, down from 608 in 2008 and 650 in 2007. About 15,000 attendees pre-registered. Last year’s show tallied 14,000 attendees. The largest industrial tool trade show on the East Coast, EASTEC was held May19-21 in West Springfield, MA.
by Dennis Seeds, Editor-in-Chief
digital edition
On target
For a new generation of parts, automated centerless grinding fills the bill
The taper test
Prototype fixture finds the reason why vexing toolholder wear marks appear
Watchful eye keeps tabs on 575 machine tools
Aerospace supplier sees new productivity heights, lower costs
From 12 hrs to 25 mins
Giant steps for faster cavity hogging, square-offs follow re-tooling